Warehouse Management vs Inventory Management
Table of Contents
When it comes to running a business, especially in the retail or manufacturing sectors, efficient management of both warehouse and inventory is crucial. While often used interchangeably, warehouse management and inventory management are distinct areas that serve different purposes but work in tandem to ensure smooth operations. So, what's the difference? And why is it important to understand these differences?
What is Warehouse Management?
Warehouse management refers to the processes involved in running a warehouse efficiently. This includes everything from receiving and storing products to organizing and shipping them out. It's all about optimizing the use of space and resources to ensure that products are stored and retrieved in the most efficient manner possible.
Key Functions of Warehouse Management
Warehouse management encompasses several key functions, including:
Receiving: Checking and recording incoming goods.
Storing: Organizing products in the warehouse.
Picking: Retrieving products for shipment.
Shipping: Preparing and sending out products to customers.
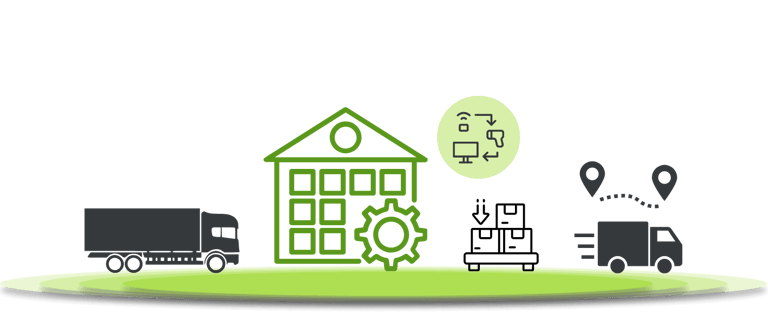
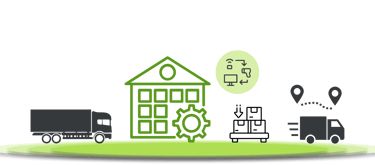
Tools and Technologies in Warehouse Management
Modern warehouse management relies heavily on technology. Warehouse Management Systems mostly are sophisticated software solutions that help manage and automate various warehouse operations. These systems often include features like barcode scanning, RFID tagging, and real-time tracking. They can operate as standalone modules or integrate into ERP systems, ensuring seamless online data transfer for precise insights into inventory status, balances, and damages.
What is Inventory Management?
Inventory management, on the other hand, focuses on tracking and managing stock levels. It involves knowing what and how many products are in stock, what is coming to the warehouse, and how much is needed to meet customer demands while accounting for seasonal fluctuations and other factors affecting stock levels. Effective management ensures that businesses maintain optimal stock levels to meet customer demand without overstocking or understocking.
Essentially, inventory management equates to money flow management because the purchased or manufactured items that are stored in the warehouse represent the business's invested capital. Efficient inventory management and turnover are crucial for optimizing working capital flow and overall business efficiency.
Key Functions of Inventory Management
Key functions of inventory management include:
Tracking Inventory Levels: Monitoring stock quantities.
Managing Inventory Levels Dynamically: Adjusting stock levels based on demand.
Replenishment: Ordering new stock to replenish inventory.
Assortment Auditing: Regularly evaluating stock composition to identify top-priority items and those ready to be discontinued.
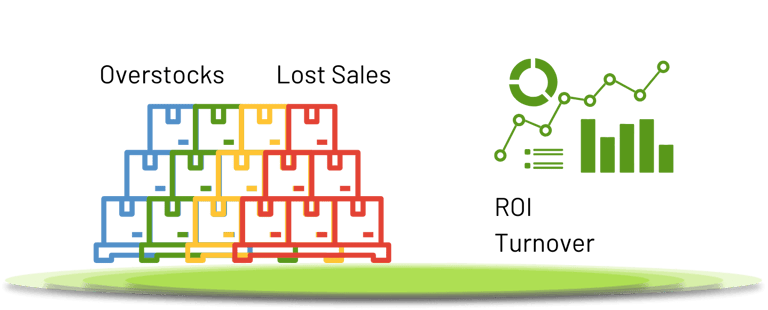
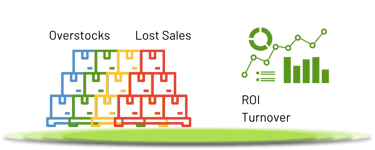
Tools and Technologies in Inventory Management
Inventory management also leverages technology, with Inventory Management Systems being the cornerstone. These systems offer features such as supply chain management, which means automated replenishment for child-plant warehouses or stores from the main-plant warehouse, automated ordering from suppliers, also assortment management insights, and inventory level alerts. Similar to Warehouse Management Systems, Inventory Management Systems can operate as standalone modules or be integrated into ERP systems.
Differences Between Warehouse Management and Inventory Management
Warehouse Management primarily focuses on the physical storage, handling, and movement of goods within the warehouse. Inventory Management focuses on tracking and managing stock levels, ensuring that the right amount of inventory is available at the right time and in the right place.
Main Factors of Warehouse Management
Inventory Storage Solutions
Effective warehouse management involves implementing storage solutions that optimize space and improve efficiency. This can include pallet racking, shelving, and automated storage systems.
Warehouse Layout and Design
The layout and design of a warehouse play a critical role in optimizing operations. A well-designed warehouse layout reduces travel time for workers, improves safety, and enhances overall productivity.
Warehouse Safety and Compliance
Safety is paramount in warehouse management. Ensuring compliance with safety regulations and standards helps prevent accidents and maintains a safe working environment for employees.
Main Factors of Inventory Management
Inventory Management Methods
There are a few well-known methods: Demand Forecasting, Min-Max, and Dynamic Buffer Management (DBM). Each method and algorithm aims to manage stock levels as accurately as possible, considering various factors. The ultimate goal is to enhance overall business efficiency.
Importance of Stock Replenishment
Modern inventory management systems track each product's stock level and send alerts when it runs low and needs attention. Depending on the inventory management method, orders for new stock are created differently: on a schedule (Demand Forecast, DBM) or when the stock reaches a certain level (Min-Max). However, the stock must be refilled to prevent stockouts and ensure the best possible customer service level. Replenishment means creating and sending orders to suppliers, which is one of the most time-consuming tasks in inventory management.
Stock Auditing and Assortment management
To understand how well inventory is being managed and to improve it, a regular stock audit is necessary. This process identifies which items are top priority and whose stock-outs are most financially damaging to the company due to missed profits caused by product absence. It also highlights slow-moving products that occupy valuable warehouse space but generate little to no profit, making them potential candidates for discontinuation. A stock audit helps categorize the assortment, allowing businesses to understand which products are more important than others and take the necessary actions to improve their management.
The Theory of Constraints in Inventory Management
The Theory of Constraints (TOC) is a management philosophy created and introduced by Dr. Eliyahu M. Goldratt. It focuses on identifying the most significant limiting factor (constraint) that stands in the way of achieving a goal and systematically improving that constraint until it is no longer the limiting factor. In the context of inventory management, TOC suggests dynamic buffer management, which controls stock and adjusts stock levels based on demand, avoiding chaos.
Dynamic buffer management differs significantly from forecasting because it doesn't rely on past data or predictions but focuses on the current situation and makes real-time adjustments. This approach ensures that the buffer—or the inventory amount on hand and on the way to the warehouse—changes dynamically to maintain optimal stock levels and meet customer needs.
Dynamic buffer management algorithms are implemented in fluentSTOCK. Users who choose fluentSTOCK for their inventory management opt for the most advanced and effective method available, with a plan “FREE” included.
The Interconnection Between Warehouse and Inventory Management
Warehouse and inventory management are interconnected but do not overlap or substitute each other as many might think. As already mentioned above, each system serves its purpose. The best and most effective way to manage the business is to have both warehouse and inventory management systems, that would ensure efficient operations in warehouses. For example, inventory management informs warehouse management about stock levels, helping to optimize storage and retrieval processes.
We hope this article has helped you understand inventory management and how it differs from warehouse management.
If you still have questions or need further clarification, please don't hesitate to contact us. We would be more than happy to discuss which solution is best for your situation.