How do supply chains work and ways to make them better?
Table of Contents
Every product you use has traveled a journey - from raw materials to the shelves where you found it. This journey is part of a supply chain that connects everything from suppliers to customers. While it might seem simple at first glance, supply chains are intricate networks that need careful management to avoid delays, high costs, and unhappy customers. Let’s break down how supply chains work and how to make them better.
What is a supply chain?
A supply chain connects all the steps needed to create and deliver a product. It starts with sourcing raw materials and ends with the final delivery to the customer. Along the way, there are several key steps:
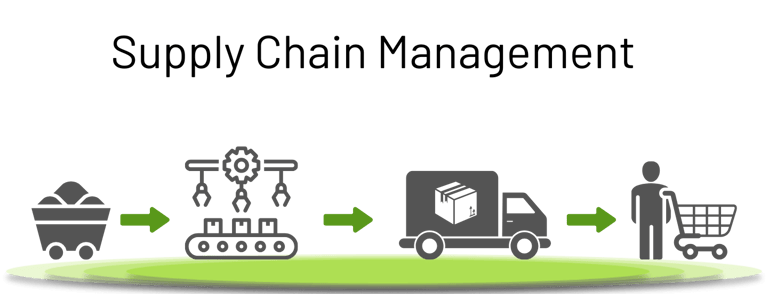
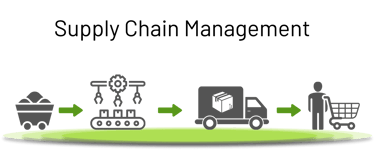
Getting materials: this is where raw materials or components are sourced from suppliers.
Making products: raw materials are turned into finished goods.
Storing goods: products are stored at different stages, like raw materials, in-process items, or finished stock.
Shipping: items are moved between suppliers, warehouses, and customers.
Distributing products: goods are sent to retailers, wholesalers, or directly to customers.
Customer support: this includes handling returns or answering questions to keep customers happy.
How does a supply chain work?
A supply chain is a series of steps that all depend on each other to work smoothly. For example, if raw materials don’t arrive on time, production slows down, and customers face delays. Everything is connected.
Imagine a situation where your warehouse is full of stock, but your stores don’t have enough to sell. That ties up cash in inventory that isn’t needed and frustrates customers who can’t find what they want. To fix this, supply chain participants - like suppliers, warehouses, and stores—must work together and communicate clearly.
Few companies manage every part of the supply chain themselves. Most rely on a network of partners, which makes teamwork and transparency even more important.
Can supply chains be improved?
Yes, and even small improvements can make a big difference. Better supply chain management can reduce costs, speed up processes, and keep customers coming back. Here are practical steps to improve your supply chain:
Make everything clear:
Use tools to track where your inventory is and what’s happening with your shipments. When you can see the whole picture, it’s easier to spot and fix problems.
Use real-time data for demand management:
Monitor sales and trends as they happen. Dynamic Buffer Management (DBM) is great for this because it adjusts inventory levels automatically to match demand. That way, you avoid running out of stock or holding too much.
Balance your assortment:
Don’t let your shelves get overstuffed, but don’t leave them empty either. Review your assortment regularly and make small adjustments to match customer needs.
Build strong supplier partnerships:
Reliable suppliers make a big difference. Work with partners you can trust to deliver on time and help solve problems.
Simplify shipping:
Look for ways to combine shipments, optimize delivery routes, and choose efficient carriers. These changes can save money and time.
Use technology wisely:
Tools like order tracking, inventory management systems, and warehouse management systems help control processes and ensure a smooth flow in your warehouses and supply chain. Start small and scale up as you see results.
Implement KPIs that matter:
Track things like delivery times, inventory turnover, and order accuracy. These numbers show where you’re doing well and where you can improve.
Be ready for surprises:
Disruptions happen, so plan ahead. Work with multiple suppliers and keep a small backup stock (safety buffers) of important products to stay prepared.
Why does teamwork matter?
Supply chains only work well when everyone involved communicates and collaborates. If suppliers, warehouses, and retailers aren’t on the same page, delays and mistakes can pile up. By sharing information and aligning goals, the whole system becomes more reliable.
Extra Tips for Success
Think green: reducing waste, streamlining routes, and sourcing responsibly not only helps the planet but also improves your reputation with customers.
Listen to your customers: pay attention to what they want and adjust your supply chain to meet their needs. A supply chain only succeeds when the end customer buys the product. Simply moving products through the supply chain isn’t enough. Everyone involved should focus on doing their part well to ensure the customer at the very end is satisfied. Happy customers come back.
Build a better supply chain
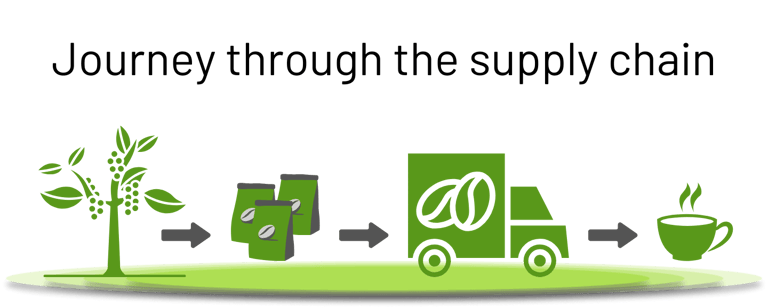
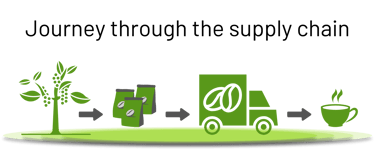
Supply chains are all about getting products from their raw beginnings to the hands of customers. Imagine the journey of a coffee bean: it starts on a farm, goes through processing, gets packaged, and eventually ends up in your morning cup. That’s a supply chain at work.
These systems can get pretty complex. They involve many steps, including sourcing materials, manufacturing, storing goods, shipping, and selling. And they’re often long, with different companies, different countries, and people working together to keep everything moving.
For the supply chain to run smoothly, every participant needs to play their part. This means communicating clearly, sharing updates, and solving problems quickly. When everyone works together efficiently, customers get what they need, and businesses succeed.
The Fluentstock tool follows DBM principles and efficiently manages even the most complex and extended supply chains.
If you have any questions about FluentSTOCK functionality and how it helps you to manage your business supply chain, please contact us to discuss further.